Tales from the Joist End
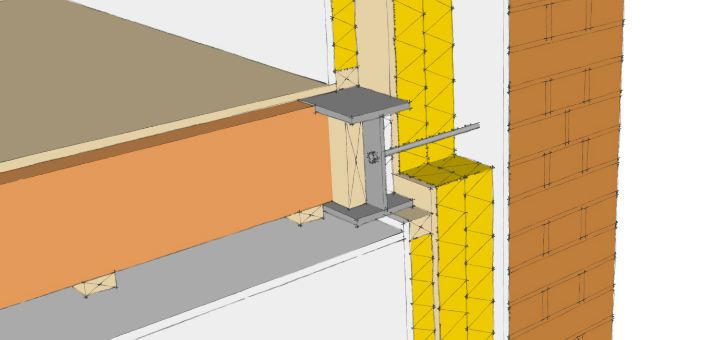
Retrofit projects require careful detailing to secure the necessary energy efficiency improvements without compromising the building fabric.
In the second of our articles on retrofit, we’re going to take a closer look at just one detail. It will help to demonstrate the complexity behind delivering ‘deep’ retrofits, something we identified in our last article as a major barrier to its broad roll-out across the UK. The detail in question is the ‘joist end’, where the timber beams supporting the floors of a house meet the masonry wall. Although every house is different, the traditional detail is for this timber joist to sit embedded in the brickwork, concrete or stone that forms the wall.
Key to understanding retrofit is predicting how the addition of insulation will affect the way moisture moves through the envelope of the house.Why is this detail important? Key to understanding retrofit is predicting how the addition of insulation will affect the way moisture moves through the envelope of the house. External wall insulation (EWI) is relatively straightforward because by adding a new layer to the outside of the wall we provide additional protection from rain whilst the joist ends stay in the warm and dry. With Internal Wall Insulation (IWI), it’s a different kettle of fish. Adding insulation to the inside face of the wall moves the joist ends into the colder part of the structure where they’re vulnerable to damp. Damp and timber aren’t good bedfellows.
The good news is that lots of designers have already tried to tackle the problem. The Retrofit for the Future programme funded by the government’s Technology Strategy Board (now Innovate UK), carried out a number of test projects to kick-start the retrofitting of the UK’s social housing stock. These case studies are published in Marion Baeli’s excellent book ‘Residential Retrofit’ (1). I’ve extracted the ‘joist end’ details from three of the case studies which used IWI to demonstrate different approaches to the challenge. All three retrofit projects attempt to provide sufficient insulation meet the standard needed by 2050. i.e. an 80% reduction in CO2 emissions.
1. ‘Pickle It’ : The Preservative Approach
The Easton Road project in Bristol was a retrofit of a Victorian mid-terrace house with solid brickwork walls. The front elevation was insulated internally to maintain the Victorian character of the façade. With 260mm of mineral wool insulation, the joist ends were well and truly embedded in the cold part of the wall. The joist ends were temporarily removed from the wall and injection treated with a preservative to prolong their life. The interior face of the insulation was sealed with a vapour control layer to reduce moist air from the house reaching the joists, whilst the outside face of the wall was protected with lime render to aid breathability and minimise rainwater penetration. An MVHR system helps to control internal humidity levels too. As a final safety measure, probes were inserted into the joist ends to monitor moisture levels in the joist ends to assess the risks of rotting.
2. ‘Off with their Heads’ : Bespoke Joist Hangers
At the Midmoor Road project in London, the front elevation was internally insulated due to planning requirements and to retain the attractive streetscape. The shell was stripped right back to the solid brickwork walls allowing good access to the joists. To reduce the risk of decay in the joist ends, they were trimmed to the inside face of the wall and suspended with bespoke joist hangers. Whilst the timbers still penetrate the three layers of rigid insulation, the joists ends sit within a ventilation gap to control moisture. Humidity passing from within the house is limited by an OSB vapour control layer and the property was fitted with an MVHR system.
3. ‘Look No Hands’ : Steel Channel and Basalt Fibre Wall Ties
The Princedale Road project in London was the first residential retrofit in the UK to be certified to the Passivhaus standard. To achieve the demanding energy efficiency standards, the insulation and air-tightness layers had to be continuous. For this reason, the designers took the decision to support the joists ends in-board of the insulation with a new steel beam spanning between the party walls. This brings the joist end entirely within the heated envelope of the dwelling to minimise any risk of decay. The front wall of the house, separated from the internal floor, is restrained with basalt fibre wall ties. Of course, the opportunities for carrying out the same detail in the adjoining properties will be limited by the structural capacity of the party wall.
These three solutions give a flavour of how careful detailing can provide high levels of energy efficiency improvements without compromising the building fabric. A focus on the joist end is deliberate here, but don’t forget that retrofit requires a holistic approach to the whole building and it’s systems.
Read more articles about Retrofit on Tracing Green here.
References:
(1) All three projects are described in Marion Baeli’s excellent book ‘Residential Retrofit : 20 Case Studies‘, 2013, by RIBA Publishing.
Easton Road Project by White Design Ltd., page 60
Midmoor Road Project by Prewett Bizley Architects, page 40
Princedale Road by Paul Davis + Partners, page 28